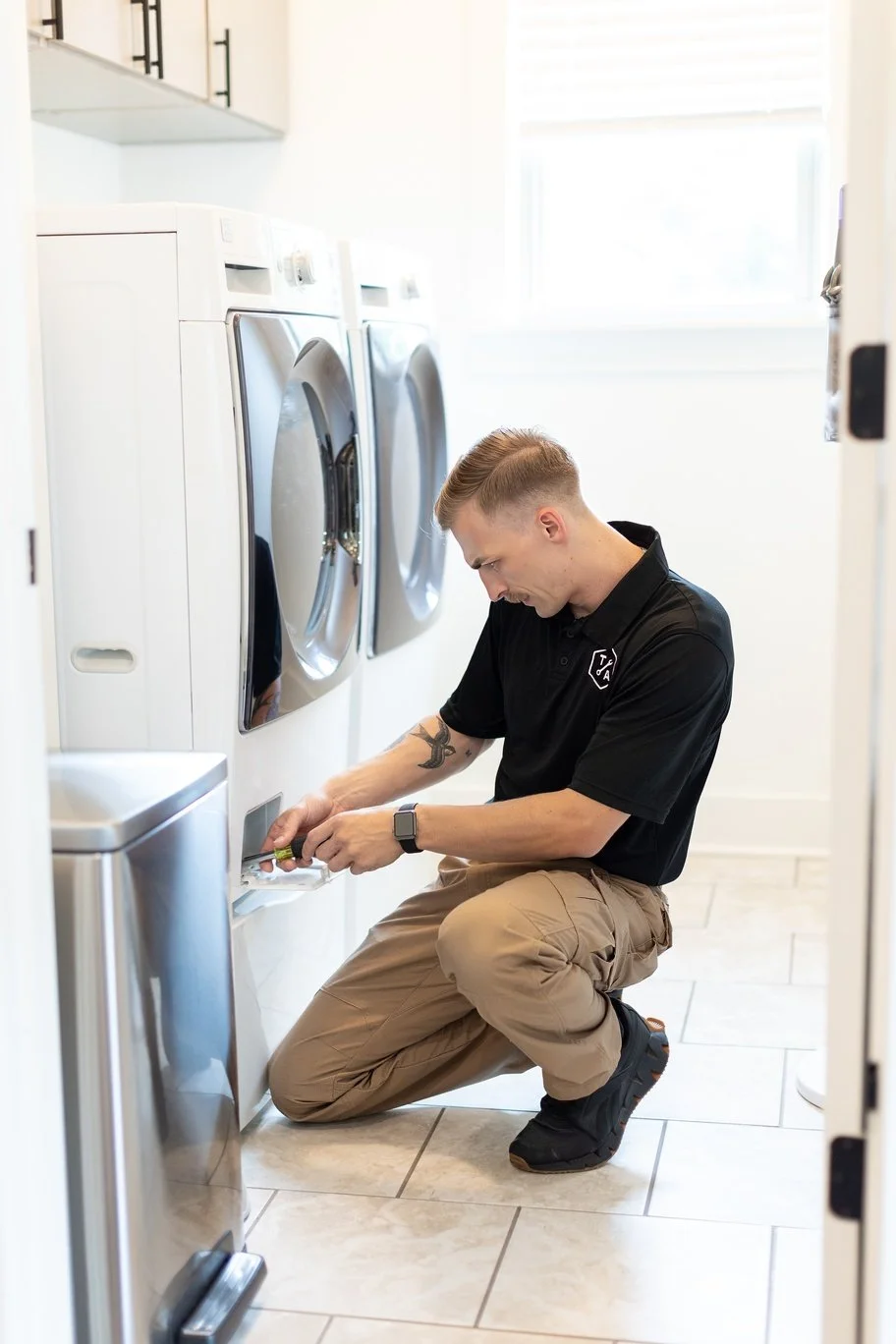
Washer Repair in Fultondale, AL
A washing machine plays a big role in keeping household routines on track. When it stops draining, refuses to spin, or makes unusual noises, laundry can quickly pile up. Common problems include a broken lid switch, worn drive belt, clogged pump, or faulty control board. Each of these can interrupt normal cycles and reduce cleaning performance. Quick action helps avoid leaks, water damage, or further wear on internal parts.
In Fultondale, AL, my washer repair services bring much-needed relief to busy households. Whether the unit is top-load, front-load, or high-efficiency, I arrive ready to diagnose the issue with care. Repair work may involve replacing a damaged part, clearing a blocked hose, or recalibrating settings. By addressing the core problem, I help bring machines back to reliable operation with minimal delay.
I focus on delivering dependable solutions that support cleaner clothes and less disruption at home. With the right parts, proper tools, and a deep understanding of washer systems, I work to restore both function and peace of mind. From loud vibrations to drainage problems, no issue is too small or complex. Fultondale residents rely on my professional repair to bring washers back into full service so laundry day doesn’t skip a beat. Whether the appliance is newer or aging, I aim to make each visit count with friendly service and expert attention.
Common Washer Problems We Fix in Fultondale
Washer won't start
When washing machines refuse to power on, I examine multiple potential causes, including electrical supply issues, faulty control boards, and door switch malfunctions. My diagnostic process begins with checking outlet voltage and circuit breakers before moving to internal components. I test lid and door switches that often prevent operation when not properly engaged as a safety feature. Start switches and timer assemblies receive thorough inspection since these components frequently develop wear from regular use. I bring replacement parts for most major brands, allowing same-day resolution for many starting problems. This comprehensive approach identifies the specific cause rather than making assumptions based solely on symptoms.
Not spinning or agitating
Movement failures significantly impact cleaning effectiveness, with several potential mechanical causes requiring systematic evaluation. I inspect drive belts for wear, cracking, or stretching, affecting their ability to transfer motor power to the wash basket. I examine motor couplings that frequently crack or break, particularly in high-capacity models subject to occasional overloading. For direct-drive washers, I test the motor, clutch, and transmission components essential for proper agitation and spin cycles. This detailed mechanical inspection identifies precisely which component prevents proper movement, allowing targeted repairs that restore normal operation without unnecessary parts replacement or excessive labor costs.
Water not draining or overfilling
Water management problems create inconvenience and potential property damage risks requiring prompt professional attention. I inspect drain pumps, hoses, and filters for blockages or mechanical failures preventing proper water evacuation. For overfilling issues, I examine water level pressure switches, inlet valves, and control systems that regulate water flow during fill cycles. The investigation includes checking for foreign objects caught in the drainage system and examining the pump motor for electrical problems. This thorough approach addresses mechanical obstructions and electronic control issues that affect proper water level management, preventing potential flooding while restoring normal washing functions.
Leaking water
Moisture escape points require precise identification to implement effective repairs. I conduct systematic examinations, beginning with fill hoses and connections before moving to internal components like tub seals, water pumps, and door gaskets. I perform controlled testing at various cycle stages to pinpoint exactly when and where leaking occurs. This methodical approach prevents misdiagnosis that might lead to unnecessary parts replacement while failing to address the source of leakage. Following repairs, I conduct extended testing with visual inspection throughout multiple cycle stages to verify complete resolution before considering the repair complete. This attention to detail prevents recurring leaks that might cause property damage.
Loud noises or vibrations
Unusual sounds during operation typically signal mechanical problems requiring prompt attention before they escalate. I identify the specific noise type and timing to narrow potential causes. Grinding often indicates worn bearings or damaged drive components, while thumping suggests drum balance issues or foreign objects trapped in the pump. Squealing frequently results from worn belt pulleys or motor problems affecting normal rotation. I inspect suspension systems that can allow excessive movement when springs or dampening components deteriorate. For each sound type, my repair process includes isolating the specific component creating the noise rather than making assumptions, leading to targeted repairs that effectively eliminate the concerning sounds.
Door or lid won't latch
Access system failures present both convenience and functional problems since most modern washers incorporate safety interlocks, preventing operation with unsecured doors. I examine latch mechanisms, strike plates, and electronic sensors that detect proper closure. I test the control system's recognition of latch engagement, particularly in models with electronic door locks designed to prevent mid-cycle opening. For front-loading models, I inspect hinges that may sag over time, creating misalignment between latch components. This comprehensive approach identifies whether the issue stems from mechanical misalignment, component failure, or control system problems. Following repairs, I verify proper operation through multiple test cycles with various loading conditions.
Error codes on digital display
Modern washers communicate specific problems through error codes requiring professional interpretation. I understand code meanings across major brands and models, translating these indicators into specific repair strategies. When necessary, I connect diagnostic equipment to electronic control systems to access detailed fault information stored in memory. Temperature and water level sensor circuits undergo testing to verify proper function and accurate reporting to control systems. This approach allows me to address the root cause behind the error display rather than simply resetting the system temporarily. After completing repairs, I run verification cycles to confirm the complete resolution of the underlying issue that triggered the error code.
my Reviews
Benefits of Professional Washer Repair in Fultondale
-
Professional evaluation eliminates costly trial-and-error approaches that often characterize DIY repair attempts. I bring specialized diagnostic equipment, including electrical testing meters, pressure gauges, and manufacturer-specific tools for precise problem identification. This technical capability combines with extensive training and experience across thousands of service calls to recognize patterns in symptoms that point to specific underlying causes. My diagnostic process follows manufacturer-recommended procedures, systematically evaluating each potential failure point rather than making assumptions. This methodical approach saves time and money by identifying which components require attention without unnecessary replacements or wasted labor hours pursuing incorrect solutions that fail to resolve the original problem.
-
When washing machines malfunction, household routines face significant disruption that I’m prepared to resolve quickly. I arrive equipped with commonly needed parts for major brands, eliminating delays caused by waiting for components to be ordered and delivered. My repair process follows efficient workflows developed through years of hands-on experience, allowing most repairs to be completed during a single visit. I prioritize prompt service, offering appointments often within 24-48 hours of initial contact. For urgent situations involving water leaks or complete system failure, I provide expedited scheduling whenever possible. This responsive approach minimizes inconvenience and restores normal laundry capabilities without the extended downtime often experienced with less experienced providers.
-
Professional repairs often provide significant savings compared to replacing an appliance, especially for higher-end models with substantial initial costs. I offer honest assessments of repair versus replacement options, taking into account both immediate expenses and long-term reliability. When repairs make sense, I leverage access to quality parts at wholesale prices and efficient repair techniques to keep costs reasonable without sacrificing workmanship. For older machines, I discuss potential reliability concerns and recommend cost-effective solutions that extend the appliance’s useful life without unnecessary spending. This balanced approach helps homeowners make informed financial decisions based on accurate information about their washer’s condition, repair costs, and expected lifespan after service.
-
Professional maintenance and timely repairs significantly extend appliance lifespan beyond typical expectations. When I service your washer, I don’t just fix the immediate issue—I also look for early signs of wear on belts, hoses, and bearings to recommend preventative replacements before costly breakdowns occur. I carefully calibrate water level controls, balance the spin system, and verify cycle timing to reduce mechanical stress and avoid premature wear. After completing repairs, I provide practical maintenance tips that help keep your machine running smoothly and prevent repeat problems. This comprehensive care approach often adds years of reliable service, maximizing the value of your appliance investment.
My Washer Repair Process in Fultondale
Choose Tucker Appliance Repair for Washer Repair in Fultondale, AL
-
As a resident of the greater Birmingham area myself, I bring unique local insights to every service call in Fultondale. I understand the region’s water quality challenges, common power fluctuations in specific neighborhoods, and other local factors that can affect your washer’s performance and lifespan. I’m familiar with the washer models most commonly found in Fultondale homes, which helps me diagnose issues faster and complete repairs more efficiently. Being based nearby means I can respond quickly to washing emergencies, often arriving within hours rather than days. My deep community ties mean I focus on providing personalized service and building lasting relationships—not just completing transactions. This local expertise offers a level of care and responsiveness that national chains with rotating technician rosters simply can’t match.
-
Financial transparency is a cornerstone of my service approach, starting with clear communication about diagnostic fees, hourly rates, and parts pricing. I provide comprehensive estimates before any work begins, ensuring there are no unpleasant surprises when the final invoice arrives. The detailed cost breakdown clearly distinguishes between essential repairs and optional improvements, empowering homeowners to make informed decisions about the scope of service. My competitive pricing reflects fair market rates without compromising quality through inferior parts or rushed workmanship. When repairs approach replacement cost thresholds, I offer honest assessments of repair versus replacement options, respecting client decisions either way. This straightforward approach builds trust and allows homeowners to plan confidently for necessary washer maintenance without concern over escalating costs.
-
I represent Tucker Appliance Repair and hold industry-recognized certifications reflecting my technical knowledge and professional capabilities. I maintain a selective hiring process focused on proven appliance repair experience, technical aptitude, and customer service orientation essential for positive service experiences. The ongoing education program keeps me current with evolving washer technologies and manufacturer-specific repair techniques across all major brands servicing Fultondale homes. I participate in formal training programs covering mechanical systems and increasingly complex electronic controls in modern washing machines. This commitment to technical excellence translates to efficient, accurate repairs regardless of washer type, age, or complexity, with most problems resolved during the initial visit without repeat service calls.
-
My service commitment extends beyond completing repairs to establishing lasting relationships built on reliability and exceptional results. Every repair includes my workmanship guarantee, ensuring the job was completed correctly using proper techniques and quality components. Should any concerns develop following service completion, my responsive follow-up process addresses issues promptly without additional charges for related problems. This customer-centered approach has earned hundreds of positive reviews from satisfied Fultondale homeowners across multiple platforms. I regularly survey clients after service completion to identify improvement opportunities and maintain high satisfaction ratings. This dedication to excellence reflects my understanding that reputation represents my most valuable business asset in the close-knit Fultondale community, where word-of-mouth recommendations drive my continued growth.
Schedule washer Repair
When washing machines malfunction in Fultondale, AL, and neighboring communities, Tucker Appliance Repair delivers prompt, professional solutions for all brands and models. I bring specialized diagnostic equipment and manufacturer-specific knowledge to every service call. Homeowners experiencing problems with starting, spinning, draining, or unusual noises can often contact my local office for same-day scheduling. With transparent pricing, quality replacement parts, and comprehensive service guarantees, Tucker Appliance Repair has established itself as the region’s trusted source for dependable washer repairs. My thorough approach addresses immediate symptoms and underlying causes, providing lasting solutions that extend appliance life while restoring normal laundry operations with minimal disruption.