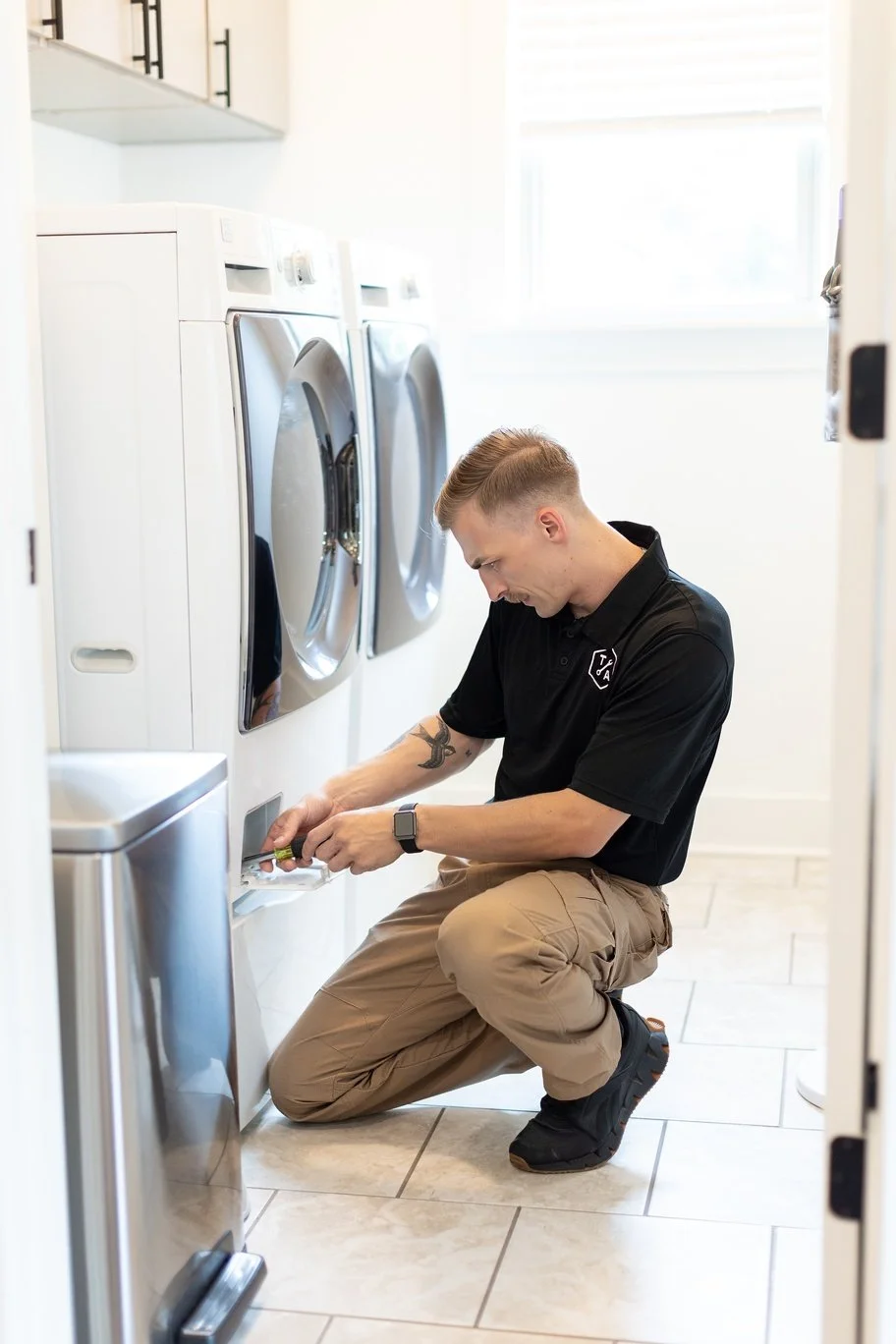
Dryer Repair in Moody, AL
Dryer repair in Moody, AL, helps keep daily routines running without interruption. When a dryer stops producing heat, takes too long to dry, or fails to start altogether, laundry can back up quickly. I provide reliable repair services to restore convenience without the hassle of replacing the appliance. From basic mechanical issues to more complex electrical faults, my expertise makes a noticeable difference.
I handle many dryer problems, including loud noises, poor airflow, and sensor errors. Each repair begins with a thorough inspection to identify worn-out parts, faulty wiring, or blocked ventilation. Whether dealing with electric or gas dryers, I use tools and techniques tailored to the specific issue and machine type. Heating elements, thermostats, and belts are common areas of concern that often require replacement or adjustment.
I’m proud to support households in Moody with efficient and courteous service that brings dryers back to peak performance. A well-functioning dryer helps reduce energy waste, minimize drying time, and keep clothing fresh and ready when needed. Clean vents and properly calibrated sensors also contribute to home safety. With experience and a thoughtful approach, I help dryers work quietly, reliably, and consistently.
Common Dryer Problems We Fix in Moody
Dryer won't start
When dryers fail to power on, I examine multiple potential causes, including electrical supply issues, faulty door switches, and control board malfunctions. The diagnostic process begins with checking outlet voltage and circuit breakers before moving to internal components. I test thermal fuses that often trip due to overheating conditions, preventing dryer operation as a safety measure. Start switches and timer assemblies receive thorough inspection since these components frequently develop wear from regular use. I carry replacement parts for most major brands, allowing same-day resolution for many starting problems. This comprehensive approach identifies the specific cause rather than making assumptions based solely on symptoms.
Dryer not heating
Heating failures are the most common complaint among dryer owners, with several potential causes requiring professional diagnosis. I systematically evaluate heating elements, thermal fuses, high-limit thermostats, and gas valve solenoids, depending on the dryer type. For gas dryers, I inspect igniters and flame sensors that might prevent proper combustion. Electric models undergo resistance testing across heating circuits to identify failed components. I also examine wiring connections that can loosen over time due to vibration and thermal cycling. This methodical process allows me to pinpoint exactly which component requires replacement, restoring proper heating function without unnecessary parts replacement.
Dryer takes too long to dry clothes
Extended drying cycles often indicate airflow restrictions that reduce efficiency and increase operating costs. I inspect the entire ventilation pathway, from lint traps to exterior vent outlets, identifying restrictions that impede proper airflow. I examine dryer vent hoses for kinks, compression, or lint buildup that restricts exhaust movement. Inside the dryer, I check blower wheels for lint buildup or damage that affects air movement capacity. The heating element function is also verified to confirm proper temperature maintenance throughout the drying cycle. This comprehensive approach addresses mechanical and maintenance issues that contribute to prolonged drying times.
Dryer making strange noises
Unusual sounds during operation typically signal mechanical problems requiring prompt attention before they escalate. I identify the specific noise type and timing to narrow potential causes. Squealing often indicates worn belt pulleys or idler assemblies, while thumping suggests drum support issues or foreign objects trapped in the drum. Scraping noises frequently result from worn drum glides or bearing assemblies that support rotational movement. I inspect motor mounts that can allow excessive movement when deteriorated. For each sound type, my repair process includes isolating the specific component creating the noise rather than making assumptions, leading to targeted repairs that effectively eliminate the concerning sounds.
Dryer won't spin/tumble
Rotation problems significantly impact drying effectiveness, requiring a thorough mechanical system evaluation. I inspect drive belts for wear, cracking, or stretching that affect their ability to transfer motor power to the drum. The motor receives electrical testing to verify proper function and winding integrity. I examine idler pulleys that maintain proper belt tension, as these components often develop bearing failures that prevent smooth operation. For direct-drive models, I inspect coupling assemblies between motors and drums. This detailed approach identifies the specific mechanical component preventing proper tumbling, allowing targeted repairs that restore normal rotation without unnecessary parts replacement.
Burning smell from the dryer
Odors indicating overheating or burning require immediate professional attention due to potential fire hazards. I first inspect lint traps and vent systems for significant accumulations that restrict airflow and create overheating conditions. I examine heating elements for signs of damage or deterioration that might cause localized hot spots. Electrical connections throughout the appliance receive inspection for signs of arcing or overheating. The blower housing area undergoes thorough cleaning to remove lint buildup, which frequently contributes to burning odors. This priority service addresses the immediate safety concerns and underlying maintenance issues that created the condition.
Dryer shuts off unexpectedly
Unexpected cycle termination often indicates safety system activation or control failures requiring diagnostic expertise. I examine thermal overload protectors that interrupt operation when excessive temperatures develop. Cycling thermostats undergo testing to verify proper temperature regulation that prevents premature shutdowns. I inspect moisture sensors that might inaccurately detect dry conditions, particularly when corrosion or residue affects their sensitivity. The main control board receives a thorough examination for signs of component failure or programming errors. This systematic approach identifies whether mechanical safety devices, electronic controls, or power supply interruptions cause unexpected shutdowns.
Error codes on digital displays
Modern dryers communicate specific problems through error codes requiring professional interpretation. I understand code meanings across major brands and models, translating these indicators into specific repair strategies. When necessary, I connect diagnostic equipment to electronic control systems to access detailed fault information stored in memory. Temperature and moisture sensor circuits undergo testing to verify proper function and accurate reporting to control systems. This approach enables me to address the root cause behind the error display rather than simply resetting the system temporarily. After completing repairs, I run verification cycles to confirm the complete resolution of the underlying issue.
My Dryer Repair Services in Moody
-
Our comprehensive evaluation process examines all dryer systems to identify both reported issues and potential developing problems. We test electrical circuits using specialized meters measuring voltage, resistance, and current flow under operating conditions. Mechanical components undergo visual inspection and operational testing to identify wear patterns or alignment issues. We perform combustion analysis for gas dryers to verify proper fuel ignition and safe exhaust characteristics. Electronic control systems receive detailed examinations using manufacturer-specific diagnostic modes that reveal stored error codes and operating history. This thorough approach provides a complete understanding of the appliance's condition beyond addressing the immediate problem.
-
Restoration of proper heating function requires precise diagnosis and quality replacement components. Our technicians test resistance across heating circuits to identify failed elements or damaged wiring. We examine high-limit thermostats and cycling thermostats that control temperature regulation for electric dryers. Gas model service includes inspection of ignition systems, gas valve solenoids, and flame sensors critical to safe operation. When replacement proves necessary, we install manufacturer-approved heating assemblies rated for the specific model, maintaining proper airflow patterns and temperature ranges. This attention to component matching prevents future compatibility issues while restoring full heating capability.
-
The mechanical drive system needs specialized tools and techniques to access and service properly. Our technicians evaluate motor function through current draw analysis and winding resistance measurements that reveal electrical health. We inspect and lubricate bearing assemblies supporting the drum structure, replacing worn components that create excessive friction or alignment problems. Drive belts receive tension adjustment or replacement based on condition assessment, using proper installation techniques that prevent premature wear. For front-loading models, we examine door seal integrity and hinge stability that affect drum alignment. This comprehensive mechanical service restores quiet, efficient operation while extending the appliance's lifespan.
-
Electronic system repairs require technical knowledge and specialized equipment to diagnose and resolve effectively. Our technicians examine control boards for signs of component deterioration, particularly around heat-generating elements and power supply sections. We test temperature and moisture sensors under operating conditions to verify accurate reporting to the main control system. Button assemblies and selector switches undergo resistance testing to identify deterioration causing intermittent function. When replacement proves necessary, we perform complete system reinitialization and calibration procedures recommended by manufacturers. This detailed electronic service restores reliable program selection and accurate cycle control.
-
Proper airflow maintenance significantly impacts performance and safety. Our technicians utilize specialized brushes and vacuum systems to remove lint accumulation from internal ductwork and blower housings inaccessible through normal cleaning. We inspect flexible vent hoses for damage or compression that restricts proper exhaust flow. We examine exterior vent flaps for wall-mounted ductwork for proper operation and freedom from obstruction. The cleaning process includes removing and thoroughly cleaning lint trap assemblies, including the housing area where lint frequently bypasses the screen. This preventative service improves drying efficiency while significantly reducing fire risk associated with lint accumulation.
-
Quality component installation requires proper parts selection and correct installation techniques. Our technicians utilize manufacturer-approved replacement components designed for each model, maintaining original performance specifications and safety ratings. We keep a comprehensive inventory of commonly needed parts in our service vehicles, allowing same-day repairs for the most common issues. Installation procedures follow manufacturer guidelines regarding torque specifications, alignment requirements, and proper sequence to prevent damage during assembly. All electrical connections receive proper termination techniques to prevent future failures due to loose connections or corrosion. Complete operational testing verifies proper function across all cycles and programs following installation.
My Reviews
Dryer Brands We Repair in Moody
Our Dryer Repair Process in Moody
Schedule Your Service Appointment
When homeowners contact our service center, our scheduling team collects specific information about the dryer model and symptoms experienced to prepare for the visit properly. We offer flexible appointment windows, including same-day service for urgent situations involving potential safety concerns. The scheduling process includes pre-visit troubleshooting suggestions that might restore function while waiting for the technician's arrival. Our staff provides clear expectations regarding arrival times, service duration, and preliminary cost information based on reported symptoms. This thoughtful scheduling approach demonstrates respect for clients' time while allowing our technicians to arrive prepared with needed parts and equipment for efficient service delivery.
In-Home Diagnosis & Inspection
Upon arrival, our technicians conduct systematic examinations, beginning with a visual inspection of external components before proceeding to internal systems. We utilize specialized diagnostic equipment, including multi-meters, thermal imaging tools, and manufacturer-specific electronic interfaces, to collect precise performance data. Inspection involves operating the dryer through various cycles while monitoring electrical consumption, heat production, and mechanical function. Our technicians examine the immediate problem area and related systems that might contribute to the reported symptoms. Throughout this process, clear communication with homeowners.
Choose Tucker Appliance Repair for Washer Repair in Moody, AL
-
As longtime residents of Moody and surrounding communities, our repair specialists bring hometown knowledge to every service call. We understand the specific challenges affecting local appliances, from hard water issues to power fluctuations common in certain neighborhoods. Our deep community roots translate to personalized service focused on building lasting relationships rather than completing transactions. Tucker Appliance Repair maintains active involvement in local business associations and community events, demonstrating our commitment to the area we serve. When neighbors call for dryer repair, they receive service from technicians who understand appliance repair's technical aspects and Moody residents' expectations for quality workmanship and professional conduct.
-
Our technical team possesses comprehensive knowledge spanning diverse dryer manufacturers and models, eliminating guesswork from the repair process. We regularly participate in manufacturer training programs that keep our skills current with evolving technology and design changes. This broad expertise allows us to service everything from basic budget models to sophisticated units featuring smart home integration and specialized fabric care cycles. Our parts inventory includes components compatible with all major brands, facilitating same-day repairs in many situations. The depth of our cross-brand knowledge proves particularly valuable when diagnosing unusual problems that might confuse technicians with limited experience across multiple manufacturers and generations of appliances.
-
Transparency forms the cornerstone of our business approach, beginning with clear communication about service fees and repair costs before any work begins. Our detailed estimates provide complete information about parts, labor, and additional services required to restore proper function. We present multiple repair options when available, explaining the benefits and limitations of each approach without pressure tactics or rushed decisions. The pricing structure remains consistent regardless of neighborhood or home value, reflecting our commitment to fair treatment for all clients. This straightforward approach eliminates unpleasant surprises when the final invoice arrives and allows homeowners to make informed decisions about repair versus replacement based on accurate cost information.
-
Our commitment to exceptional service begins with the first phone call and extends through every interaction with our company. We respect appointment times, arrive within the promised window, and maintain clear communication if unexpected delays occur. Our technicians present themselves professionally, wearing clean uniforms and using protective materials to safeguard home surfaces during repairs. The repair process includes clear explanations in non-technical language, helping homeowners understand what happened and how repairs will resolve the issue. Following service completion, our follow-up process checks satisfaction and addresses any questions that might arise. This client-centered approach has earned hundreds of positive reviews from satisfied Moody homeowners across multiple platforms.
Schedule Dryer Repair
When dryers malfunction in Moody, AL, and neighboring communities, Tucker Appliance Repair delivers prompt, professional solutions for all brands and models. The company's certified technicians bring specialized tools and manufacturer-specific knowledge to every service call. Homeowners experiencing extended drying times, strange noises, or complete system failures can often contact Tucker's local office for same-day scheduling. With transparent pricing, quality replacement parts, and exceptional workmanship, Tucker Appliance Repair has established itself as the region's trusted source for dependable dryer repairs. Their comprehensive service approach addresses immediate concerns and underlying issues to provide lasting solutions for residential laundry equipment.