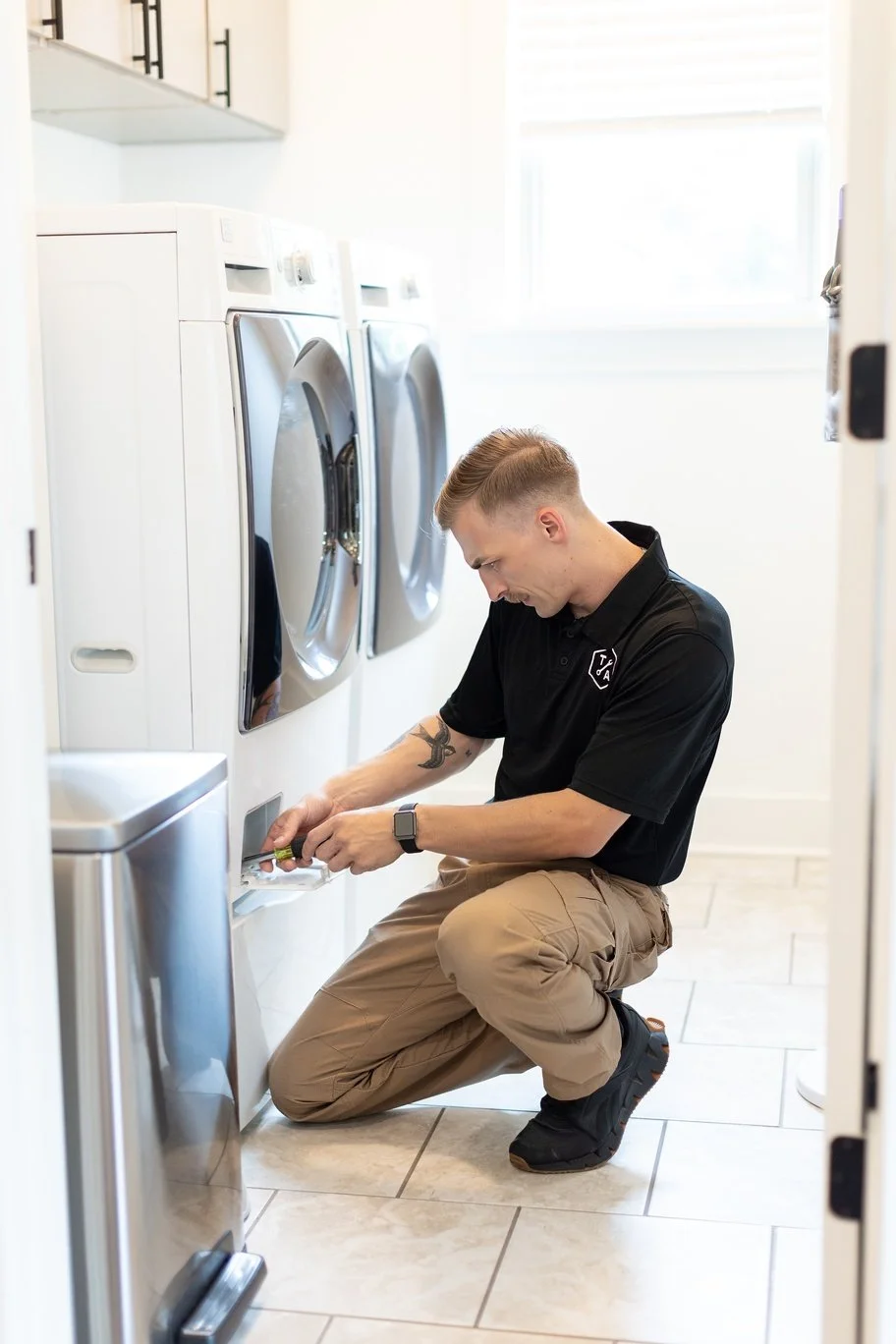
Dryer Repair in Fultondale, AL
A dryer that stops working correctly can slow down an entire household routine. Clothes may come out damp, cycles may run too long, or strange noises might start to develop. Common culprits include a faulty heating element, a broken belt, damaged sensors, or a clogged vent. Over time, even well-maintained dryers can show signs of wear interrupting daily laundry cycles.
In Fultondale, AL, my dryer repair services offer prompt, dependable help when appliances stop performing as they should. I work with gas and electric models, identifying the issue through detailed inspection and using the right tools for every job. Whether it’s a worn drum roller, malfunctioning thermostat, or electrical short, repairs are completed with accuracy and care to bring machines back to optimal function. Timely service helps avoid longer drying times and prevents heat-related safety risks.
I work with a friendly approach and a focus on effective repair that restores confidence in daily routines. With each visit, parts are inspected, cleaned, and replaced when needed to keep the dryer operating safely and efficiently. Fultondale households rely on my dependable repair services to bring back the convenience of warm, dry clothes without the frustration of repeated loads. Whether the issue is minor or more involved, my goal remains to deliver dryer repairs that keep homes running smoothly.
Common Dryer Problems I Repair in FultondalE
Dryer not heating
When dryers run but fail to produce heat, I systematically evaluate multiple potential causes to identify the specific issue. I test heating elements, thermal fuses, high-limit thermostats, and cycling thermostats that regulate temperature for electric models. For gas dryers, I inspect igniter systems, flame sensors, gas valve solenoids, and thermal components that control proper combustion. Using specialized testing equipment, I verify electrical continuity and resistance values to reveal component failures that may not be visible during visual inspection. This methodical approach prevents misdiagnosis and unnecessary parts replacement while addressing the true source of heating failure. Many Fultondale households attempt temporary fixes by adjusting settings, which might mask underlying issues requiring professional attention.
Dryer won't turn on
Complete power failure in dryers often stems from electrical supply problems or internal component failures requiring professional diagnosis. I verify the proper voltage at the outlet or junction box before examining household circuit breakers that might have tripped. The investigation continues with testing internal fuses, door switches, smart switches, and control boards that manage startup functions. For electronic models, I inspect ribbon cables and connection points that frequently develop intermittent issues affecting reliable operation. This systematic process identifies whether the problem exists in home electrical systems or within the appliance. My repair strategy targets the specific failed component rather than unnecessarily replacing multiple parts, saving both time and expense for Fultondale homeowners.
Drum not spinning
Rotation failures significantly impact drying effectiveness, with several potential mechanical causes requiring systematic evaluation. I inspect drive belts for wear, cracking, or stretching that affect their ability to transfer motor power to the drum. I examine idler pulleys and tensioners that maintain proper belt alignment and pressure during operation. Motor testing includes electrical verification and bearing inspection to identify issues affecting power delivery to the drive system. For direct-drive models, I inspect coupling assemblies between motors and drums. This detailed mechanical inspection identifies precisely which component prevents proper movement, allowing targeted repairs that restore normal operation without unnecessary parts replacement or excessive labor costs that might otherwise be incurred.
Dryer makes loud or unusual noises
Concerning noises during operation typically signal mechanical problems requiring prompt attention before they escalate into major failures. I identify the specific noise type and timing to narrow potential causes. Scraping often indicates worn drum slides or support rollers while rumbling suggests bearing failures in idler pulleys or motor assemblies. Squealing frequently results from belt issues or inadequate lubrication in moving parts. I inspect mounting brackets and support structures that can loosen over time, creating excessive movement during operation. For each sound type, my repair process includes isolating the specific component creating the noise rather than making assumptions, leading to targeted repairs that effectively eliminate the concerning sounds before they lead to more extensive damage.
Dryer shuts off too soon or runs too long
Inconsistent cycle timing creates significant convenience issues and often indicates developing component failures. For premature shutdowns, I examine thermal limiters, cycling thermostats, and electronic control systems that might incorrectly detect completion or overheating conditions. When dryers run excessively long, I inspect moisture sensors, heating elements, and ventilation systems that affect efficient moisture removal. The diagnostic process includes evaluating airflow patterns through the entire exhaust path from the lint trap to the exterior vent outlet. This comprehensive approach identifies whether the problem stems from component failures, maintenance issues like lint accumulation, or installation problems affecting proper ventilation. My solutions address immediate cycle timing problems and underlying causes affecting overall efficiency.
Burning smell from the dryer
Odors indicating overheating or burning require immediate professional attention due to potential fire hazards. I first inspect lint traps and vent systems for significant accumulations that restrict airflow and create overheating conditions. I examine heating elements and thermostats for signs of damage or deterioration that might cause localized hot spots. Electrical connections throughout the appliance receive inspection for signs of arcing or overheating that can produce distinctive burning odors. Motor bearings undergo evaluation for excessive wear that might create friction and heat during operation. This safety-focused approach addresses the immediate concern and underlying maintenance issues that created the condition. My repair solutions prioritize restoring safe operation while providing recommendations to prevent the recurrence of similar problems.
Clothes not drying properly
When garments remain damp after normal cycles, multiple potential causes require systematic investigation. I evaluate heating systems to verify proper temperature maintenance throughout the drying cycle. I inspect moisture sensors and electronic controls that determine cycle completion based on remaining dampness levels. Airflow testing examines the entire ventilation pathway for restrictions that prevent efficient moisture evacuation. For condenser models, I inspect heat exchanger systems and condensate drainage paths essential for proper function. This comprehensive approach distinguishes between issues caused by component failures, maintenance needs, or improper usage patterns. My repair solutions address the specific cause of drying inadequacy while optimizing overall performance for consistent results across various load types and sizes.
Error codes or digital display issues
Modern dryers communicate specific problems through error codes requiring professional interpretation. I understand code meanings across major brands and models, translating these indicators into specific repair strategies. When necessary, I connect diagnostic equipment to electronic control systems to access detailed fault information stored in memory. Temperature and moisture sensor circuits undergo testing to verify proper function and accurate reporting to control systems. Display panel issues receive an evaluation, including connection verification and component testing, to determine whether problems exist in the display or the main control board driving it. This technical approach allows me to address the root cause behind error displays rather than temporarily resetting the system.
my Reviews
my Dryer Repair Process in Fultondale
-
When Fultondale residents contact my service center, my friendly scheduling process collects essential information about the dryer model and specific problems experienced. This preparation allows me to arrive with appropriate diagnostic tools and likely needed parts. I offer flexible appointment windows, including same-day service for urgent situations affecting daily household routines. The scheduling process includes preliminary troubleshooting suggestions that might restore basic functions while awaiting professional service. Clear communication about arrival times demonstrates respect for clients' valuable time, with confirmation calls before arrival providing narrow timeframes rather than extended waiting periods. This thoughtful scheduling approach represents the first step in my customer-focused service experience.
-
Upon arrival, I conduct systematic examinations following manufacturer-recommended diagnostic procedures specific to each dryer type and model. I utilize specialized testing equipment, including digital multimeters, airflow gauges, and gas pressure meters appropriate for the specific appliance. The diagnostic process includes operating the dryer through various test cycles while monitoring electrical consumption, heat production, and mechanical function. I examine the immediate problem area and related systems that might contribute to the reported symptoms. Throughout this process, clear communication with homeowners provides an understanding of findings without technical jargon that might cause confusion or uncertainty about necessary repairs.
-
With repair authorization, I immediately begin work using manufacturer-approved parts and industry-standard techniques. I maintain a well-stocked service vehicle containing commonly needed components for most major brands, facilitating same-visit repairs for many issues. My repair protocols follow manufacturer guidelines regarding proper disassembly sequence, component alignment, and reassembly procedures that preserve original operating characteristics. Throughout the repair process, I maintain an organized work area and protect surrounding surfaces from potential damage. This professional approach reflects my commitment to quality workmanship that addresses not just symptoms but underlying causes of appliance malfunction, preventing the recurrence of similar problems in the future.
-
Before considering any repair complete, I perform comprehensive operational testing across multiple cycles and settings. This verification process examines electrical safety, proper heating function, mechanical operation, and control system performance under actual working conditions. I measure key parameters, including exhaust temperature, airflow volume, and cycle timing, to confirm proper operation within manufacturer specifications. For gas dryers, additional testing includes combustion analysis and ventilation verification, which are critical to safe operation. I thoroughly clean the work area after successful testing, removing all packaging materials and replacing parts and service-related debris. This attention to detail extends beyond the repair to the entire service experience.
-
My commitment continues after the repair concludes. Within a few days of service completion, I personally follow up with clients to confirm satisfaction with the repair quality and service experience. This communication allows me to address any questions about proper operation or maintenance recommendations. I maintain detailed service records for each client, building a comprehensive maintenance history that aids in future diagnostics if ever needed. Should any concerns arise following my service, I stand ready to address them promptly, demonstrating my dedication to lasting customer relationships built on quality workmanship. All repairs include my workmanship guarantee, providing peace of mind regarding service quality with prompt follow-up should any issues develop.
Dryer Brands I Repair in Fultondale
Choose Tucker Appliance Repair for Dryer Repair in Fultondale, AL
-
As a member of the greater Birmingham community, I bring hometown values to every service call in Fultondale. I understand local residents' specific needs and expectations through years of building relationships throughout the area. My deep community roots translate to personalized service focused on lasting customer satisfaction rather than maximizing service volume or revenue. Being locally owned means direct accountability, with me personally involved in maintaining service quality rather than following distant corporate policies. I maintain active involvement in community events and organizations, demonstrating my commitment to the region beyond simply providing repair services. This strong local presence allows rapid response when dryer problems disrupt important household routines or weekly laundry schedules.
-
As the owner and sole repair specialist at Tucker Appliance Repair, I hold industry-recognized certifications reflecting my technical knowledge and professional capabilities. My background includes proven appliance repair experience, strong technical aptitude, and a customer service approach focused on delivering positive service experiences. I maintain all required licensing and safety certifications mandated by state regulations for gas appliance work. Through ongoing education, I stay current with evolving dryer technologies and manufacturer-specific repair techniques across all major brands serving Fultondale homes. This commitment to technical excellence means I can deliver efficient, accurate repairs regardless of dryer type, age, or complexity — with most problems resolved during the initial visit.
-
Transparency forms the cornerstone of my business approach, beginning with clear communication about service calls and potential repair costs before scheduling appointments. My detailed estimates provide complete information about parts, labor, and any additional services required without hidden charges or unexpected additions when the final invoice arrives. The pricing structure remains consistent regardless of neighborhood or home value, reflecting my commitment to fair treatment for all clients. I present multiple repair options when available, explaining the benefits and limitations of each approach without upselling unnecessary services or replacements. This straightforward approach builds trust and allows homeowners to make confident decisions about dryer maintenance and repairs based on accurate information.
-
My confidence in repair quality manifests through comprehensive warranty coverage that protects Fultondale homeowners following service completion. All replacement parts installed by me carry manufacturer warranties typically ranging from ninety days to one year, depending on component type. My workmanship guarantee extends beyond parts to cover the installation and adjustment work performed during repairs, with prompt follow-up service provided should any related issues develop. This protection applies to all dryer types and brands serviced, demonstrating my commitment to lasting repair solutions rather than temporary fixes. The detailed documentation provided for the following service clearly outlines warranty terms and contact procedures should questions arise, giving peace of mind regarding immediate repair quality and future performance.
Schedule Dryer Repair
Tucker Appliance Repair delivers prompt, professional solutions for all brands and models when dryers malfunction in Fultondale, AL, and neighboring communities. As the owner and sole certified technician, I bring specialized diagnostic equipment and manufacturer-specific knowledge to every service call. Homeowners experiencing heating problems, unusual noises, or clothes that remain damp after complete cycles can often contact my local office for same-day scheduling. With transparent pricing, quality replacement parts, and comprehensive service guarantees, Tucker Appliance Repair has established itself as the region's trusted source for dependable dryer repairs. My thorough approach addresses immediate symptoms and underlying causes, extending appliance life while restoring normal laundry operations with minimal disruption.